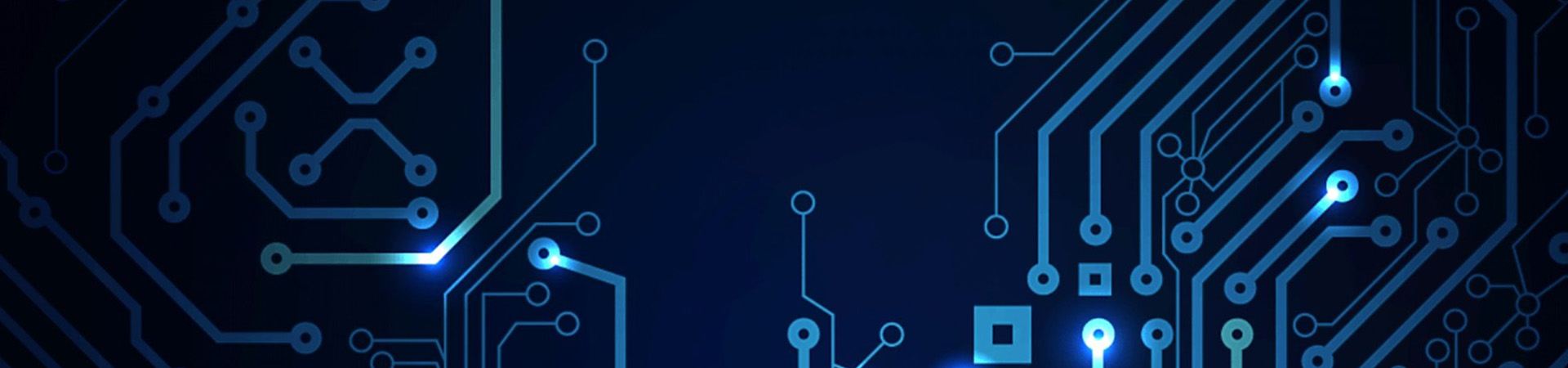
Pre-Production Engineering Steps for PCB Fabrication
Pre-Production Engineering Steps for PCB Fabrication
For PCB Fabrication orders, pre-production engineering focuses on validating design accuracy and manufacturability. This includes reviewing Gerber files, verifying drill patterns, stack-up configurations, and ensuring compliance with industry standards. Once reviewed, the fabrication process begins, encompassing material preparation, layer alignment, etching, drilling, and plating to achieve precise circuit formation. Each step is carefully monitored to maintain quality and adherence to specifications before final inspection and shipment.
Here’s a detailed breakdown of the pre-production engineering steps for PCB Fabrication:
1. Data Analysis
- File Import & Initial Validation: Gerber, Excellon, and other design files are imported into our engineering system. Automated checks verify layer completeness, ensuring a solid foundation for production.
- Engineering Review: Our experts conduct in-depth analysis to validate layer consistency, copper distribution, and critical design parameters, ensuring compliance with manufacturing standards.
2. Production Tooling Preparation
- Data Security: All initial design data, including netlists and layer references, are securely archived for future quality verification.
Mechanical Adjustments:
- Drilling Data Refinement: Drill sizes are optimized to account for plating, ensuring accurate finished hole dimensions.
- Board Profile & Cut-Out Optimization: Board outlines and cut-outs are converted into machine-ready formats, incorporating breakout tabs or V-cuts for structural integrity in handling and assembly.
Layer Enhancements:
- Outer Layer Refinement: Standardize drawn features into pads and polygons, eliminating defects like pinholes or slivers to prevent shorts and opens.
- Inner Layer Optimization: Remove non-functional pads and verify thermal pad connections to reduce internal shorting risks.
- Solder Mask Adjustments: Ensure proper clearances between solder mask and copper for optimal protection.
- Silkscreen Enhancements: Adjust component markings to prevent overlap with pads, maintaining clear identification and solderability.
3. Identification Codes & Special Layers
- Traceability Codes: Integrate order-specific identifiers for tracking, compliance, and quality assurance.
- Special Layer Processing: Prepare advanced design elements like hard-gold edge connectors, peelable solder masks, and via-filling for enhanced durability and functionality.
4. Production Panelization
- Optimized Panel Layout: Circuits are efficiently arranged on production panels, incorporating tooling holes, fiducials for optical alignment, and test coupons for quality verification.
Manufacturing Enhancements:
- Drill & Route Path Optimization: Algorithms are applied to minimize drill cycles and routing time, maximizing production efficiency.
- Plating & Copper Balancing: Simulations ensure uniform plating thickness, with copper redistribution to maintain balance.
- Etch Compensation: Track widths are adjusted to counteract etching effects, preserving design accuracy.
5. Final Data Output
- Manufacturing & Testing Files: Generate precise data sets for direct imaging, drilling, profiling, and inspection—ensuring seamless execution in fabrication.
Once all pre-production verifications are completed, the PCB is cleared for fabrication. These thorough checks help:
- Ensure design accuracy and manufacturability.
- Prevent production issues by identifying potential constraints early.
- Maintain strict adherence to material and process specifications.
- Reduce defects, rework, and production delays.
By following these pre-production engineering steps, PCB Power ensures a seamless fabrication process, delivering high-quality PCBs that meet industry standards with precision and reliability.