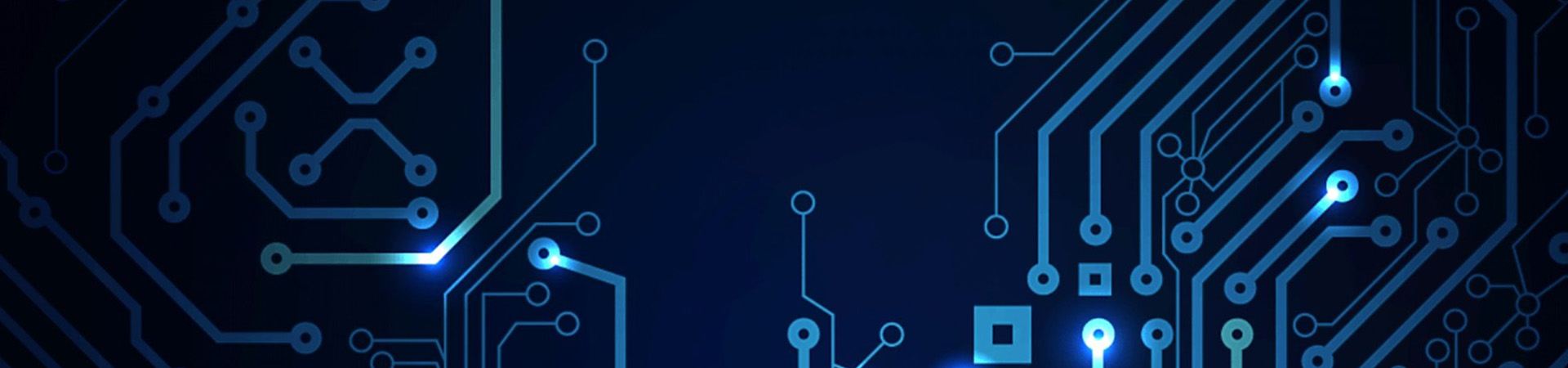
Pre-Production Engineering Steps for PCB Assembly
Pre-Production Engineering Steps for PCB Assembly
For PCB Fabrication & Assembly (F+A) orders, pre-production engineering follows a two-step approach. First, the PCB fabrication pre-production checks are performed to ensure the bare board meets design and manufacturing specifications. Once fabrication is completed, the order moves to PCB assembly pre-production, where component placement, soldering accuracy, and overall manufacturability are thoroughly verified.
Here’s a detailed breakdown of the pre-production engineering steps for PCB assembly:
1. BOM Verification
The Bill of Materials (BOM) is a critical document that lists all components required for assembly. To ensure a seamless assembly process, the BOM undergoes rigorous verification:
- PCB Footprint vs. Component Package Validation: Each component's actual PCB footprint is checked against its package dimensions to prevent misalignment or incorrect placement.This helps avoid potential soldering defects caused by mismatched footprints.
- Missing and Duplicate Component Checks: Any missing or duplicate components in the BOM are flagged to prevent assembly errors.PowerBoM automates this process, providing real-time feedback when the BOM is submitted, reducing the risk of errors before production begins.
2. Pick and Place File (CPL) Verification
The Pick and Place (CPL) file, also known as the Component Placement List, is analyzed to ensure the correct placement and orientation of components on the PCB. Key checks include:
- Layer Assignment Validation: Ensuring all components are correctly assigned to the top or bottom layer as per the design.
- Component Orientation & Rotation Check: Verifying the correct polarity and rotation of diodes, ICs, LEDs, and other polarized components to prevent incorrect placement.
- Reference Designator Matching: Confirming that each component in the CPL corresponds to the correct reference designator in the BOM to eliminate mismatches.
These validations help reduce errors during automated placement and improve overall assembly accuracy.
3. Virtual Assembly & Design for Assembly (DFA) Checks
A virtual assembly process is conducted using the CPL and BOM before the actual assembly begins. This step simulates component placement to detect potential assembly issues. Key DFA checks include:
- Package Inconsistency Detection: Identifying discrepancies between the BOM and the actual component packages before assembly to avoid misalignment and assembly failures.
- Component Spacing Verification: Ensuring proper spacing between components to:
- Prevent solder bridging and short circuits.
- Allow ease of rework and repair if needed.
- Solder Short Detection: Checking for potential solder shorts that could occur due to incorrect spacing or excessive solder paste.
- Solder Paste Verification: Ensuring proper solder paste application by checking:
- Adequate solder paste deposition - too much can cause bridging, while too little may lead to cold joints on SMD pads and test points
- Stencil alignment to avoid soldering defects due to misalignment with copper features.
- Fiducial Verification: Ensuring fiducial markers are correctly placed for machine vision alignment, preventing detection errors during automated assembly.
Once all pre-production verifications are completed, the PCB is cleared for assembly. These thorough checks help:
- Reduce manufacturing defects.
- Improve component placement accuracy.
- Ensure high-quality soldering and assembly reliability.
- Minimize costly rework and delays.
By following these pre-production engineering steps, PCB Power ensures a smooth assembly process with precision and efficiency, delivering high-quality PCBAs that meet industry standards.